Dispersive Raman for the Identification of Contaminant Particles in Ink Jet Cartridges
August 25, 2022
Introduction
The majority of printing problems are primarily caused by clogged print heads or nozzles, preventing the ink from reaching the paper. Each year billions of dollars in print cartridges are sold, thus, improving the quality and functionality of print cartridges is a priority. Several commercial inkjet cartridges were examined using the Jasco Ventuno Raman system to obtain fundamental data on the blockages of print cartridges and some knowledge as to the possible causes.
Statistics have long supported the dominance of inkjet printing. From sales of $500 million in the early 90?s to a record-breaking $14 billion in inkjet cartridge sales projected in 2001. Today, 7 out of every 10 printers sold is an inkjet. The estimated installed base of ink jet printers stands at 130 million worldwide and the numbers continue to climb.
The basic principle of the inkjet system is comprised of a reservoir of ink held in the cartridge, and a method of moving the ink from the reservoir to the paper via the print head, in a very precise and controlled procedure. Air plays an important part in the whole operation as it replaces the ink as it is used, so there must be a way for the air to get into the cartridge, while not causing the ink to drip out of the cartridge until it is required for printing. The common commercial cartridges all have air vents to allow the passage of air into the cartridge.
To get the ink onto the page, the cartridge print head has many very small (with diameters less than a human hair) nozzles or holes that allow the ink to flow to do the printing. These nozzles hold the ink until an electronic impulse causes the ink to be sent to the paper. The popular method (bubble-jet) is to selectively heat the ink at the nozzles, by resistors. As the ink heats, a bubble forms, the heat source is removed, the formed bubble “bursts” and the resulting ink is transferred to the paper. This is all happening at a very high speed, so that the dots that are being sprayed (up to 6000 per second) onto the paper will form the characters or graphics.
Another method is the “piezoelectric” method, where crystals are subjected to an electric field, which causes them to expand and contract. The movement this generates then allows a precise amount of ink to be put down onto the paper.
Experimental
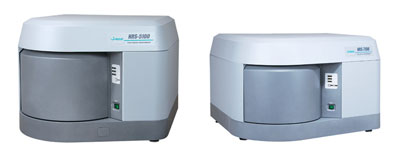
The JASCO Ventuno micro-Raman system equipped with a 532nm diode laser and two interchangeable gratings was used to collect the Raman spectra of the print cartridge. An Andor CCD detector cooled to -75C, and an integration time of 60 seconds was used for collection of sample spectra. Samples were visualized using the 100x magnification of the microscope. The Ventuno was also equipped with a MS-2000 motorized joystick controlled sample stage. The typical range for the measurement was from 470 -2,390cm-1 with a 1200g/mm grating.
Figure 1 shows a representative microscope image of one of the printer cartridge nozzles, the contamination around the nozzle clearly visible. The green spot is the laser. Three distinct particle types were collected and identified from the inside of the cartridge openings: organic matter with resolved Raman peaks; an amorphous or highly complex organic mixture, possibly carbonized due to heat; and almost pure crystalline silicon.
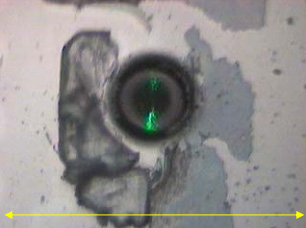
Figure 2 shows the Raman spectra from one of these particles. The organic material was identified as being polymeric with nitrogen and carboxylic groups. Amide and urea are likely candidates. However, so many organic compounds, including commercial polymers such as poly(chloroprene), have Raman lines in the 1,700-1,000cm-1 region, that making an unambiguous determination is difficult without more information on the processing.
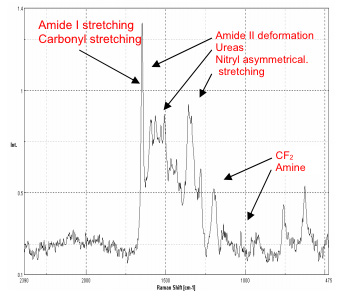
A representative microscope image of a silicon particle found in the cartridge opening is shown in Figure 3. The 2 micron green laser spot highlights the particle which is not much bigger than the laser spot. The Raman spectrum of the particle is shown in Figure 4. The first and second order peaks used to identify the silicon particle are labeled. Silicon is sometimes used in inkjets and this is a likely origin of the small silicon particles.
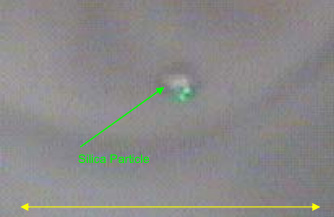
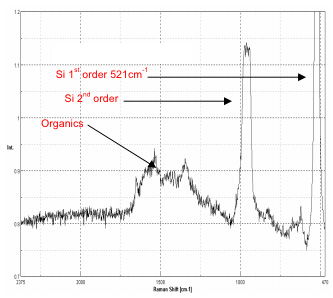
One of the major problems faced with refilling ink cartridges is the clogging of ink jets. Many black ink cartridges contain pigmented ink. Pigmented ink is not water soluble (like dye based inks) often contain solid microscopic particles of a carbon-polymer compound. The pigmented ink that remains in a cartridge forms a paste that eventually hardens and strongly adheres to the inside of the cartridge. Every printer cartridge opening that was examined contained some type of particulate matter. Most of these contaminant particles were in the micron size range. Identification of the compounds that create the blockages can lead to their elimination and make ink cartridges less susceptible to clogs.
Conclusion
The Raman spectra and representative microscope images were used to characterize the nozzle contaminants. Preliminary peak assignments for some of the organic materials were suggested and the silicon particles positively identified. Examination of the compounds that create the blockages may provide data to improve the inkjet printing mechanism and enhance the development of inkjet cartridges that are less susceptible to the clogging that plagues most systems.
Featured Products:

Dispersive Raman for the Identification of Contaminant Particles in Ink Jet Cartridges
Introduction
The majority of printing problems are primarily caused by clogged print heads or nozzles, preventing the ink from reaching the paper. Each year billions of dollars in print cartridges are sold, thus, improving the quality and functionality of print cartridges is a priority. Several commercial inkjet cartridges were examined using the Jasco Ventuno Raman system to obtain fundamental data on the blockages of print cartridges and some knowledge as to the possible causes.
Statistics have long supported the dominance of inkjet printing. From sales of $500 million in the early 90?s to a record-breaking $14 billion in inkjet cartridge sales projected in 2001. Today, 7 out of every 10 printers sold is an inkjet. The estimated installed base of ink jet printers stands at 130 million worldwide and the numbers continue to climb.
The basic principle of the inkjet system is comprised of a reservoir of ink held in the cartridge, and a method of moving the ink from the reservoir to the paper via the print head, in a very precise and controlled procedure. Air plays an important part in the whole operation as it replaces the ink as it is used, so there must be a way for the air to get into the cartridge, while not causing the ink to drip out of the cartridge until it is required for printing. The common commercial cartridges all have air vents to allow the passage of air into the cartridge.
To get the ink onto the page, the cartridge print head has many very small (with diameters less than a human hair) nozzles or holes that allow the ink to flow to do the printing. These nozzles hold the ink until an electronic impulse causes the ink to be sent to the paper. The popular method (bubble-jet) is to selectively heat the ink at the nozzles, by resistors. As the ink heats, a bubble forms, the heat source is removed, the formed bubble “bursts” and the resulting ink is transferred to the paper. This is all happening at a very high speed, so that the dots that are being sprayed (up to 6000 per second) onto the paper will form the characters or graphics.
Another method is the “piezoelectric” method, where crystals are subjected to an electric field, which causes them to expand and contract. The movement this generates then allows a precise amount of ink to be put down onto the paper.
Experimental
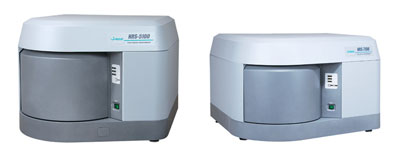
The JASCO Ventuno micro-Raman system equipped with a 532nm diode laser and two interchangeable gratings was used to collect the Raman spectra of the print cartridge. An Andor CCD detector cooled to -75C, and an integration time of 60 seconds was used for collection of sample spectra. Samples were visualized using the 100x magnification of the microscope. The Ventuno was also equipped with a MS-2000 motorized joystick controlled sample stage. The typical range for the measurement was from 470 -2,390cm-1 with a 1200g/mm grating.
Figure 1 shows a representative microscope image of one of the printer cartridge nozzles, the contamination around the nozzle clearly visible. The green spot is the laser. Three distinct particle types were collected and identified from the inside of the cartridge openings: organic matter with resolved Raman peaks; an amorphous or highly complex organic mixture, possibly carbonized due to heat; and almost pure crystalline silicon.
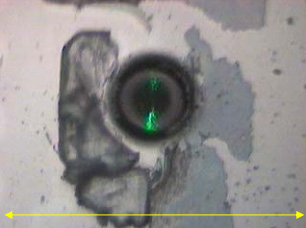
Figure 2 shows the Raman spectra from one of these particles. The organic material was identified as being polymeric with nitrogen and carboxylic groups. Amide and urea are likely candidates. However, so many organic compounds, including commercial polymers such as poly(chloroprene), have Raman lines in the 1,700-1,000cm-1 region, that making an unambiguous determination is difficult without more information on the processing.
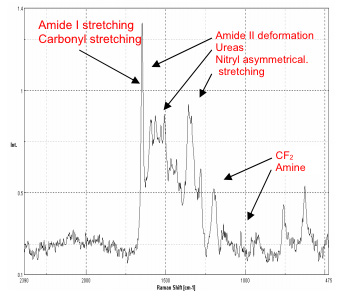
A representative microscope image of a silicon particle found in the cartridge opening is shown in Figure 3. The 2 micron green laser spot highlights the particle which is not much bigger than the laser spot. The Raman spectrum of the particle is shown in Figure 4. The first and second order peaks used to identify the silicon particle are labeled. Silicon is sometimes used in inkjets and this is a likely origin of the small silicon particles.
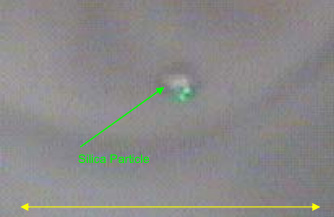
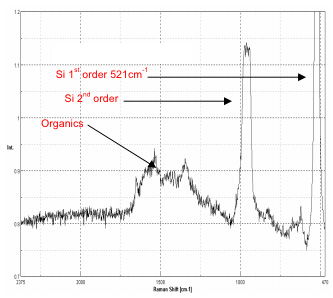
One of the major problems faced with refilling ink cartridges is the clogging of ink jets. Many black ink cartridges contain pigmented ink. Pigmented ink is not water soluble (like dye based inks) often contain solid microscopic particles of a carbon-polymer compound. The pigmented ink that remains in a cartridge forms a paste that eventually hardens and strongly adheres to the inside of the cartridge. Every printer cartridge opening that was examined contained some type of particulate matter. Most of these contaminant particles were in the micron size range. Identification of the compounds that create the blockages can lead to their elimination and make ink cartridges less susceptible to clogs.
Conclusion
The Raman spectra and representative microscope images were used to characterize the nozzle contaminants. Preliminary peak assignments for some of the organic materials were suggested and the silicon particles positively identified. Examination of the compounds that create the blockages may provide data to improve the inkjet printing mechanism and enhance the development of inkjet cartridges that are less susceptible to the clogging that plagues most systems.